Enhancing compliance and efficiency at pfm medical
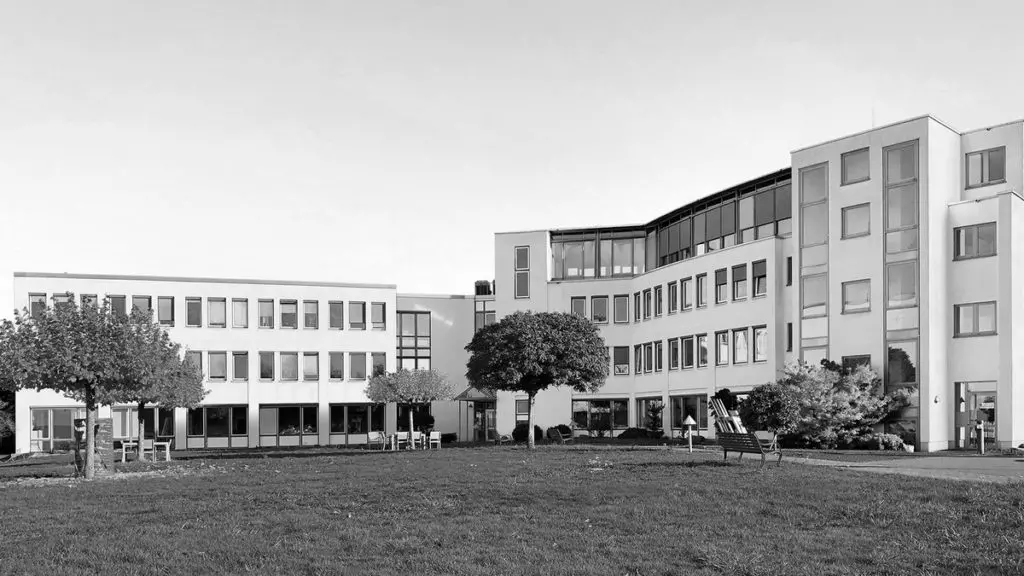
On the safe side with validatable processes in the Learning Management System

pfm medical ag is an internationally operating, medium-sized, family-owned company from Germany that offers special solutions in the healthcare sector. The company has enjoyed success in the development, manufacture and sale of quality products and has offered reliable services for nearly 50 years. Its portfolio covers the medical fields of surgery, histotechnology, cardiovascular technologies and infusion technology.
Therapeutic safety and therapeutic success are the core themes of all of pfm’s proposals. All solutions and products aim to contribute towards improving the quality of life for patients and of work quality for users.
Headquartered in Cologne, Germany, the company employs over 600 people at twelve locations worldwide.
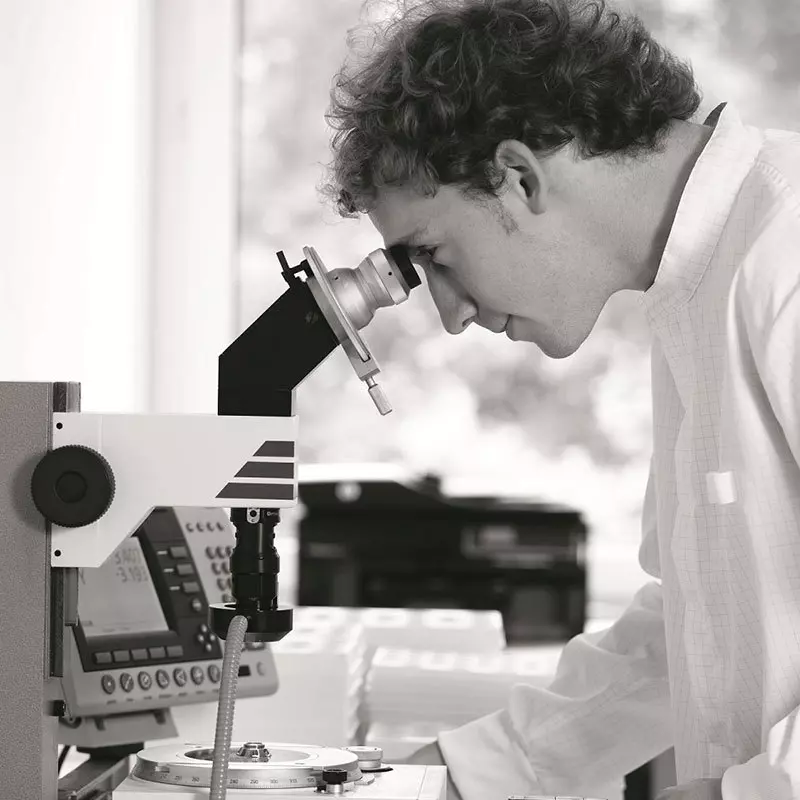
BACKGROUND
pfm medical, a medical technology company, belongs to the pharmaceutical and medical technology sector, and this 'high-risk' sector is subject to a strict obligation to document evidence of all work and training procedures.
Depending on the market they serve, these sectors are governed by the U.S. Food and Drug Administration (FDA) as well as additional regulations from the European Medicines Agency (EMA).
In addition, in 2017 the EU issued the Medical Devices Regulation (MDR) which also regulates the handling of the software used; the transition period for the MDR expires on 25 May 2021.
Comply with Medical Device Regulation without accumulating paper folders by the metre
"After just under two years, we had about ten running metres of A4 folders and had to file and enter every piece of paper by hand; that had to change". This is how Hans-Heiko Müller, Team Manager of Organisation Learning at pfm medical, describes the situation in mid-2020.
At pfm medical, the mandatory complete documentation of all training courses used to be implemented using paper records, as is still standard practice at many companies. After completing a training course, whether online or in-person, employees had to print out a paper themselves and confirm successful close-out with their signature.
The signed document was then delivered in person or by post to headquarters, where it was manually checked and entered into the existing learning management system (LMS). This was an error-prone job that tied up a lot of resources.
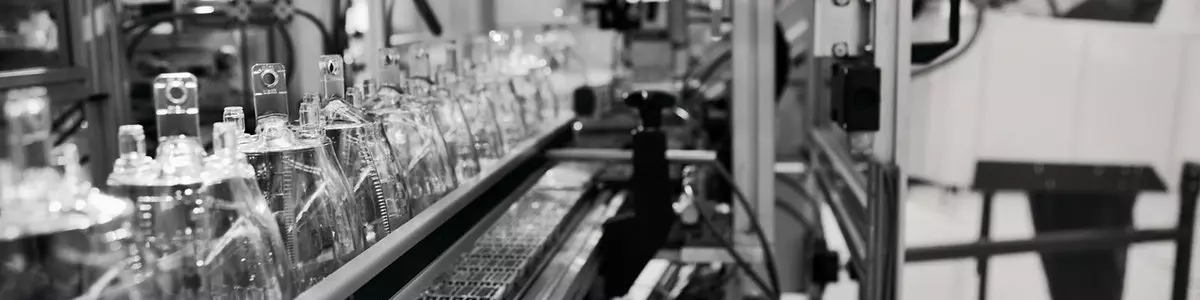
A validatable LMS in the SaaS cloud
In order to decrease the effort required for these processes while continuing to work in compliance with the rules, pfm medical decided in mid-2020 to convert the existing LMS into a validatable learning platform.
For this purpose, the company selected the imc AG Golden Master package which includes system set-up, commissioning and all updates for customers. Another special feature of the package is the validation documentation, which is provided by imc. This is the basis on which a system can be validated by the customer.
Specifically, this means that imc takes care of the overall configuration of the system and the documentation of the cloud setup. As part of this, imc documents that all the required steps for the proper installation of the system environment have been followed.
Hans-Heiko Müller explains, "In theory, we could have converted our existing LMS into a validatable system ourselves. But I would have had to have hired at least one full-time employee just for the documentation that would have been necessary at the beginning and as well as for every change and update in the future, because a few hundred pages each time add up quickly."
Of course, the topic of data security also played a major role for pfm medical. But the imc cloud solution was convincing: With a 99% guaranteed availability, certifications according to ISO 27001 and ISO 9001 and a 24/7 service time, there was nothing left to wish for. The cloud solution creates an even higher level of security than the classic paper filing system, as it is secured several times and cannot be destroyed by a fire, for example.
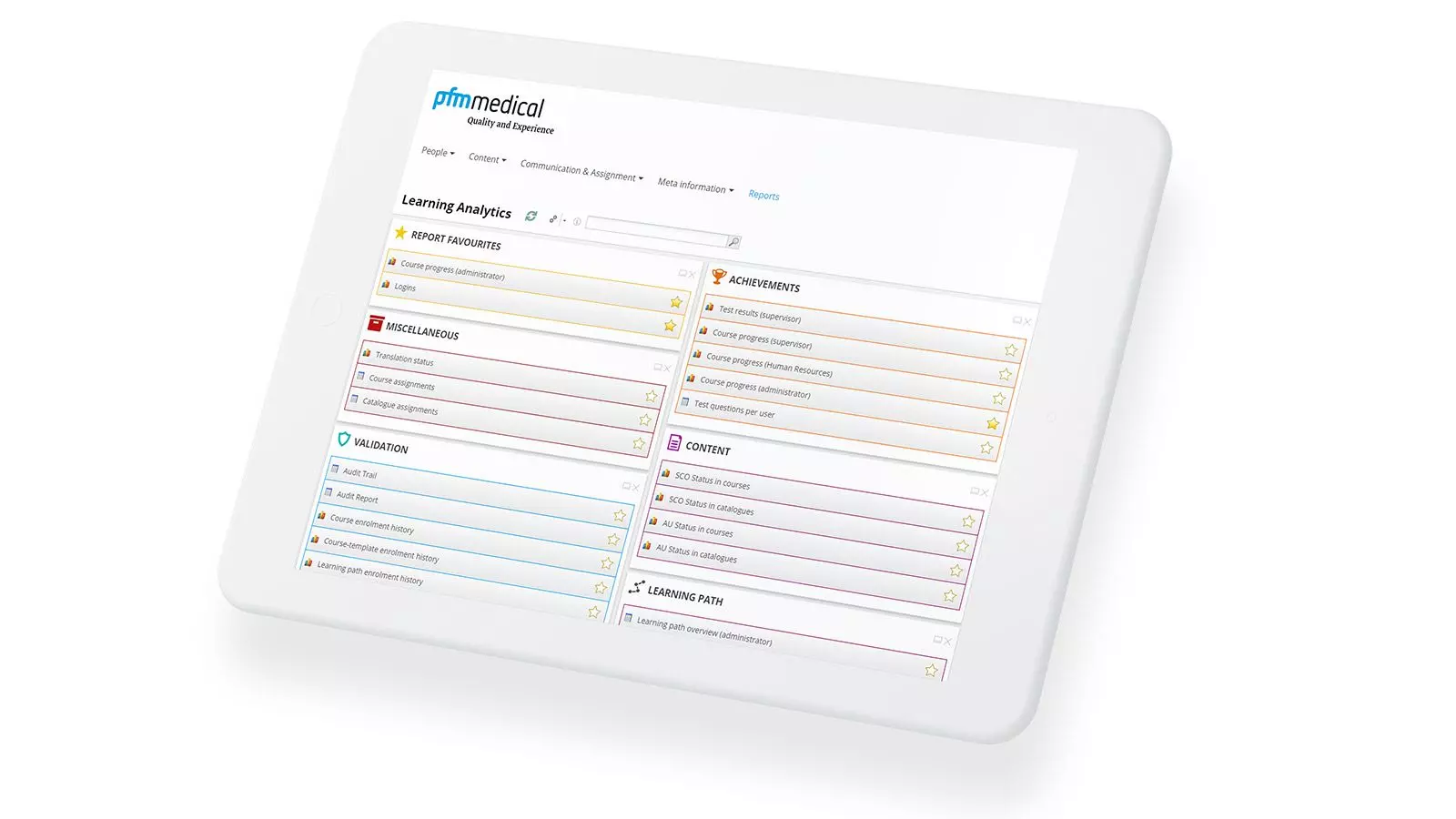
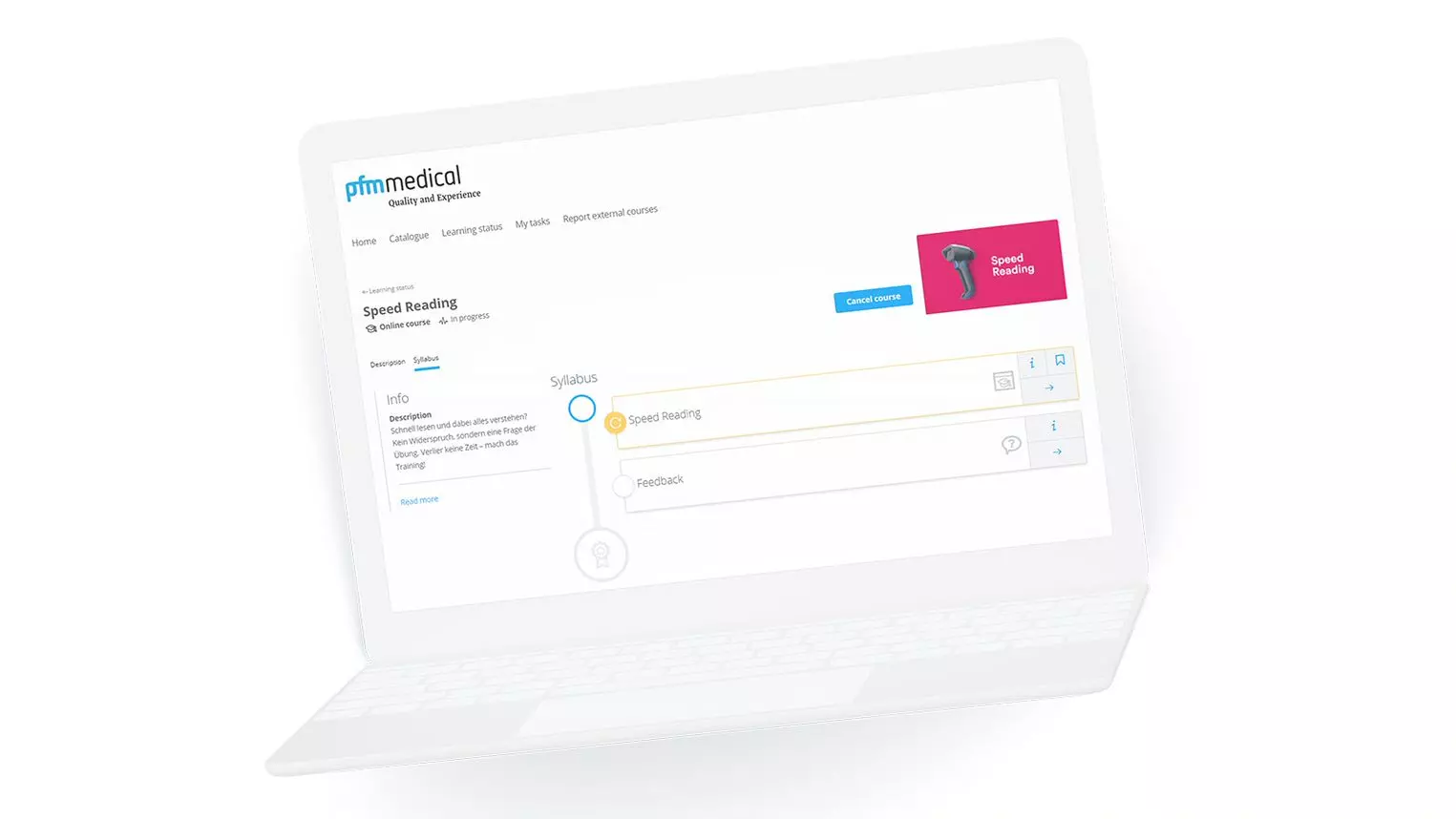
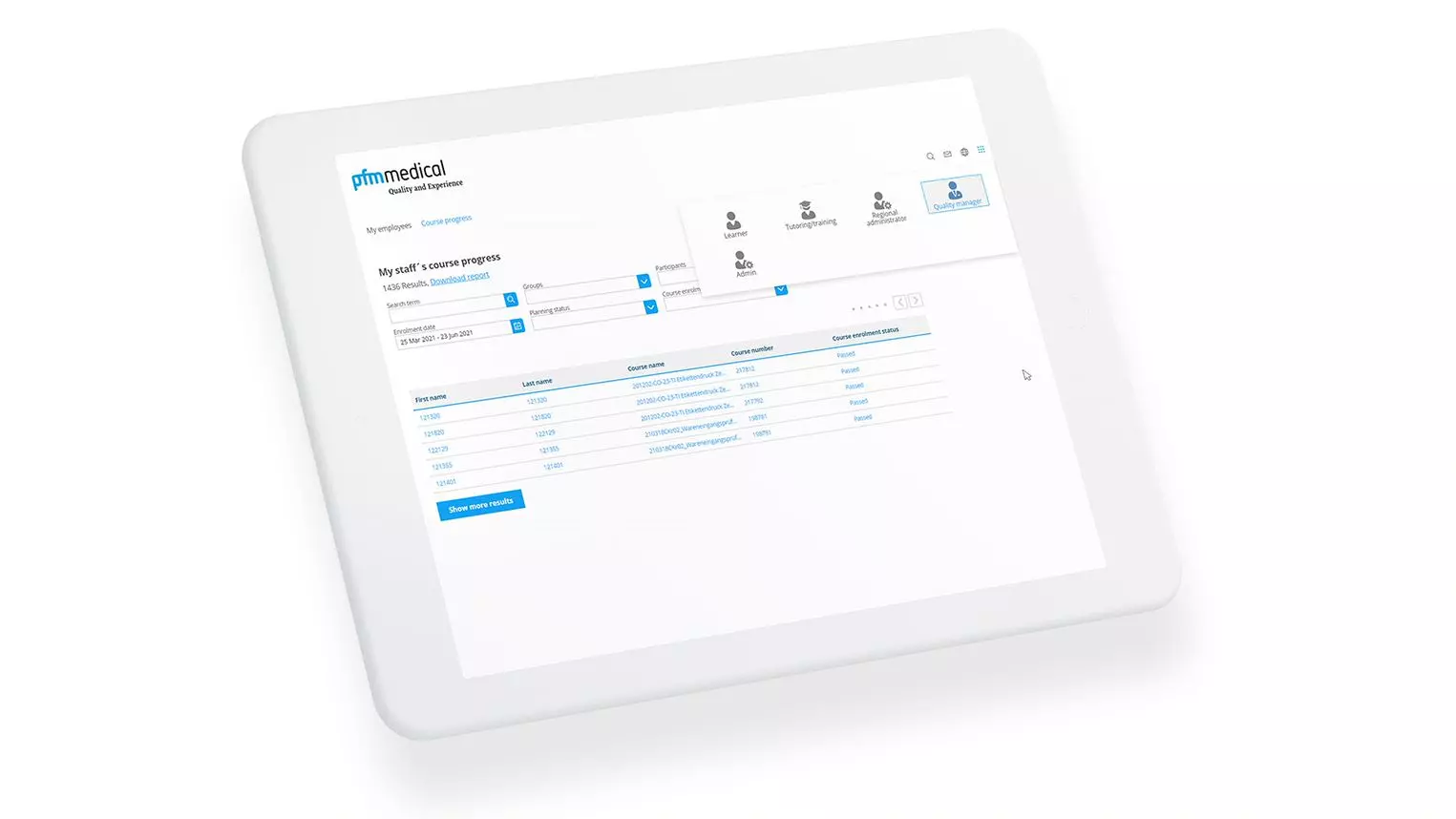
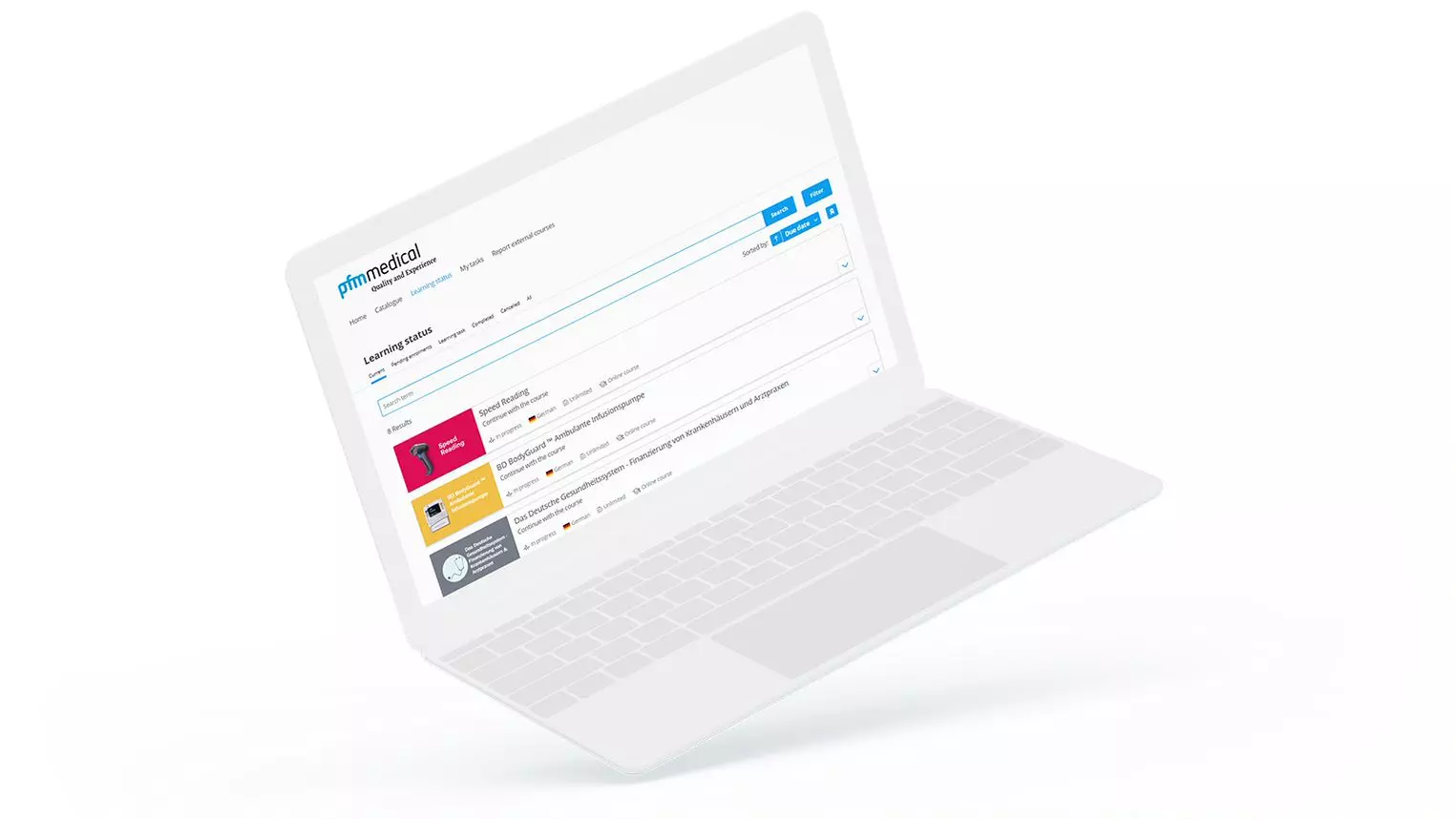
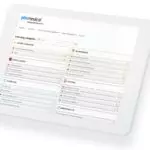
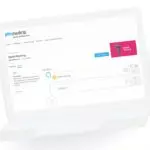
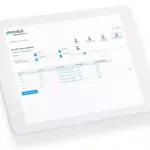
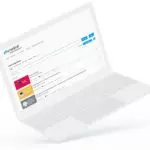
The end of the paper economy
After the successful changeover, the time had finally come; the end of the paper economy could be initiated. Instead of having to print out and sign each certificate, pfm medical employees can now enter their courses into the system themselves. All they have to do after a course close-out is confirm via e-signature that they have successfully completed the course.
In addition, entire groups of employees can be enrolled on certain learning paths together and automatically receive reminders about upcoming mandatory training courses. Although these features had already existed in the company's original LMS, regulations prevented them from being used for validation-related training.
Hans-Heiko Müller sums it up: "We learned quite a bit during the conversion process. We have adapted our processes to the system, not the other way around, and have evolved as a result. But in a way, we also had to accept that we will lose a bit of flexibility.
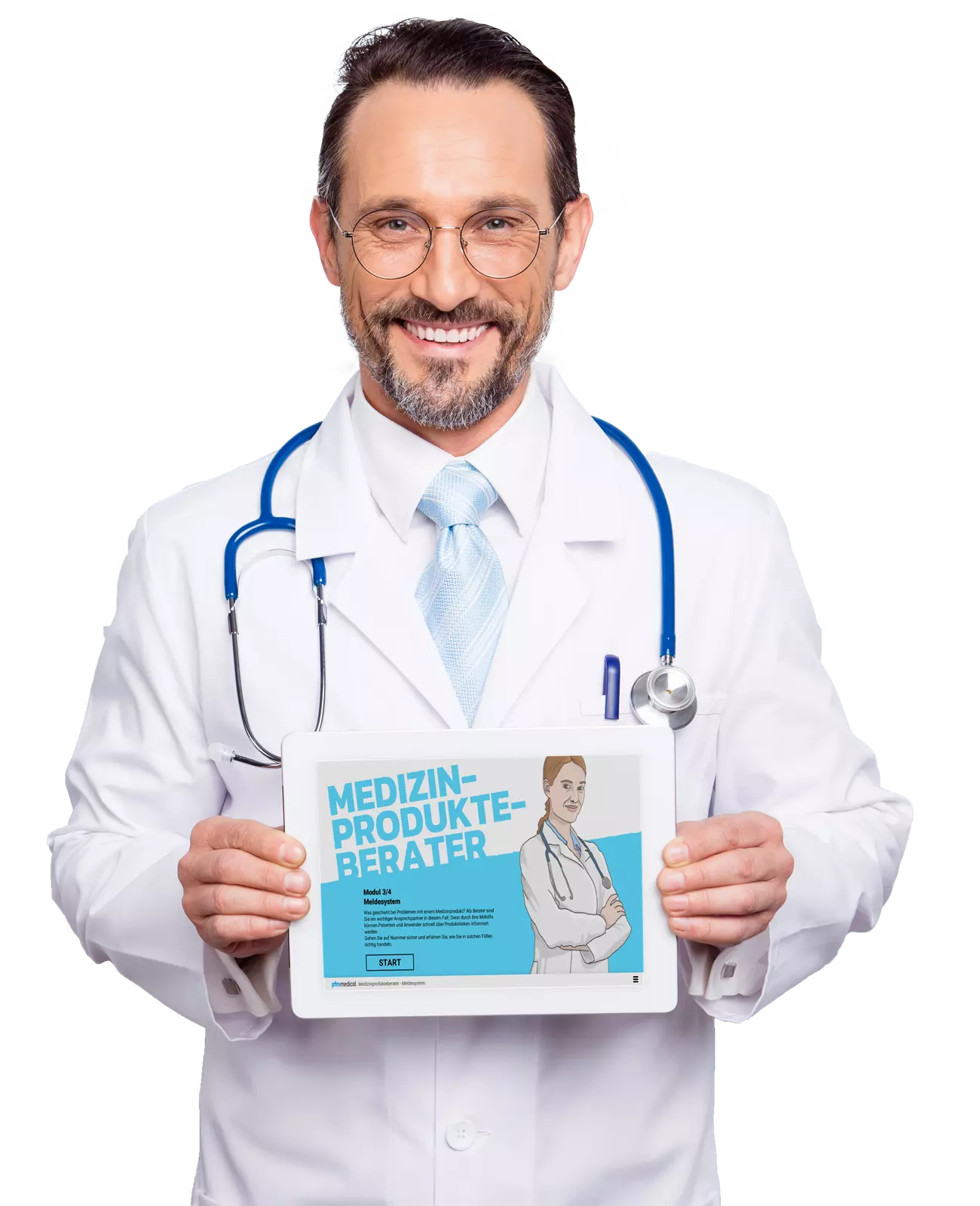
Little things that I used to change myself in 20 seconds now run through a change process and are checked and documented within the context of a four-eyes principle. The total process now takes a little longer. Still, the advantages clearly outweigh the disadvantages for the company. With the system and the documentation created by imc, we err on the side of caution during audits and save a lot of work and time at the same time in the process."
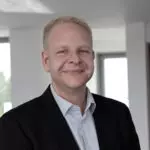